High-Rate Copper Pillar Plating
Using the Solstice® CopperMax™ Reactor
Modern semiconductor copper plating chemistries include expensive, highly engineered organic additives that serve to enhance the quality of the plating. However, these additives are readily destroyed when they come in contact with the copper anode of the plating system. This necessitates ongoing replenishment of additives and significantly increases process costs.
Our proprietary Solstice® CopperMax™ reactor integrates a cationic exchange membrane that separates organic additives from the anode while still allowing high-speed copper cation movement to the wafer. This enables higher plating rates while routinely reducing the user’s chemistry costs by more than 95% – and also delivering excellently plated feature uniformity.
Eliminating Additive Breakdown
The proprietary design of our Solstice CopperMax reactor dramatically reduces the deterioration of organic additives by using a cationic exchange membrane to keep additives from contacting the anode. This significantly reduces your chemistry costs while enhancing copper plating quality.
In other reactors, the plating behavior shifts rapidly as additives break down. The bath metrology begins to return inaccurate readings, which leads to erroneous dosing.
Applications
- Wafer level packaging
- Flip-chip interconnects
- Solder bumping (with nickel & solder plating)
- C4 bump
- Thermo-compression bonding
- And more…
Features
- Cation exchange membrane to reduce additive use
- Continuously filtered chemistry, optional carbon filtration
- High-precision wafer rotation
- Adjustable diffuser
- Dry-contact, low-maintenance plating rotor
- Customized seal reach
- Levitronix pump with LeviFlow
Benefits
- Additive costs reduced >95%
- Maximized bath life
- Extremely uniform field profile
- Seal reach aligns to existing integration
- Continuously cleaner chemistry
- Precise, consistent flow rate control
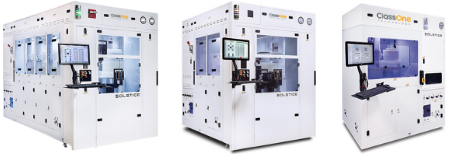
The single-wafer processing Solstice Platform is available with 8, 4, 3 or 2 chambers in customizable configurations, depending on the applications you require.
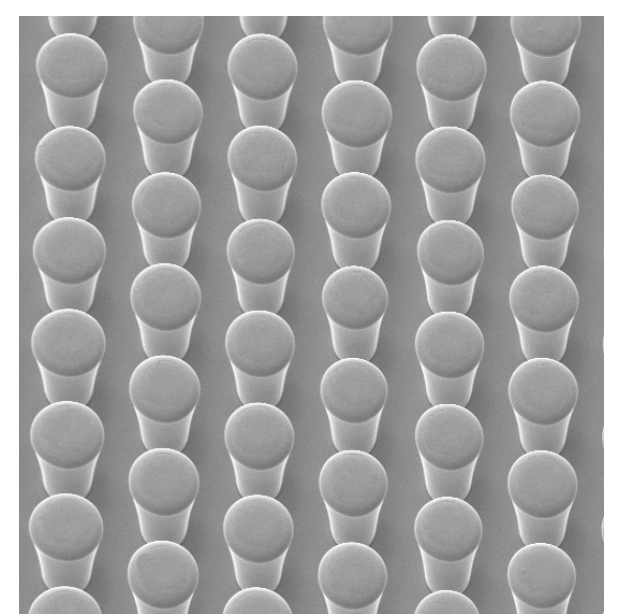
Technical Data
Wafer Sizes | 75-200mm (configurable to non-standard sizes, e.g., 160mm) |
Wafer Thickness | 150μm to >6mm |
Wafer Materials | Silicon, GaAs, GaN on Si, GaN on Sapphire, Sapphire, Transparent Substrates, and more |
Flow Rate | 25 lpm |
Plating Rate | >3μm/minute, up to 6.5μm/minute |
Within-Wafer Uniformity | <3% (range 2*mean) |
Wafer-to-Wafer Uniformity | <1% (mean-to-mean) |
CD Reduction | <0.2Å on 1200Å seed deplate |
Coplanarity | <5% |
Modern semiconductor copper plating chemistries include expensive, highly engineered organic additives that serve to enhance the quality of the plating. However, these additives are readily destroyed when they come in contact with the copper anode of the plating system. This necessitates ongoing replenishment of additives and significantly increases process costs.
Our proprietary Solstice® CopperMax™ reactor integrates a cationic exchange membrane that separates organic additives from the anode while still allowing high-speed copper cation movement to the wafer. This enables higher plating rates while routinely reducing the user’s chemistry costs by more than 95% – and also delivering excellently plated feature uniformity.
Eliminating Additive Breakdown
The proprietary design of our Solstice CopperMax reactor dramatically reduces the deterioration of organic additives by using a cationic exchange membrane to keep additives from contacting the anode. This significantly reduces your chemistry costs while enhancing copper plating quality.
In other reactors, the plating behavior shifts rapidly as additives break down. The bath metrology begins to return inaccurate readings, which leads to erroneous dosing.
Applications
- Wafer level packaging
- Flip-chip interconnects
- Solder bumping (with nickel & solder plating)
- C4 bump
- Thermo-compression bonding
- And more…
Features
- Cation exchange membrane to reduce additive use
- Continuously filtered chemistry, optional carbon filtration
- High-precision wafer rotation
- Adjustable diffuser
- Dry-contact, low-maintenance plating rotor
- Customized seal reach
- Levitronix pump with LeviFlow
Benefits
- Additive costs reduced >95%
- Maximized bath life
- Extremely uniform field profile
- Seal reach aligns to existing integration
- Continuously cleaner chemistry
- Precise, consistent flow rate control
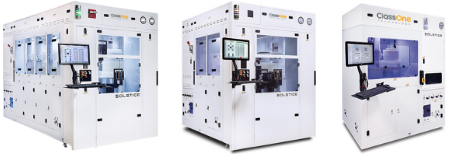
The single-wafer processing Solstice Platform is available with 8, 4, 3 or 2 chambers in customizable configurations, depending on the applications you require.