Copper RDL Plating
Using the Solstice® CopperMax™ Reactor
Copper RDL (redistribution layer) plating is a key process step in advanced packaging, requiring plating of line-and-pad features patterned in photoresist. Achieving high plating rates without sacrificing uniformity requires a high-rate copper chemistry, but it’s the chamber design that is critical to achieving both high-quality uniformity and the highest plating rates.
Our proprietary Solstice® CopperMax™ reactor integrates a cationic exchange membrane that separates organic additives from the anode while still allowing high-speed copper cation movement to the wafer. It also dramatically reduces the deterioration of organic additives by using a cationic exchange membrane to keep additives from contacting the anode. This significantly reduces your chemistry costs while enhancing copper plating quality by enabling uniform flow and density distribution of chemistry against the wafer.
The Solstice CopperMax chamber enables higher plating rates while routinely reducing user chemistry costs by more than 95% to deliver excellently plated feature uniformity.
Applications
- Wafer-level packaging
- 2.5D/3D RDL applications
Features
- Wafer rotation control
- Precision tuning of the electric field
- Conservation of costly organic additives
Benefits
- Uniform plated feature shape
- Lower chemistry costs
- Optimized cost of ownership
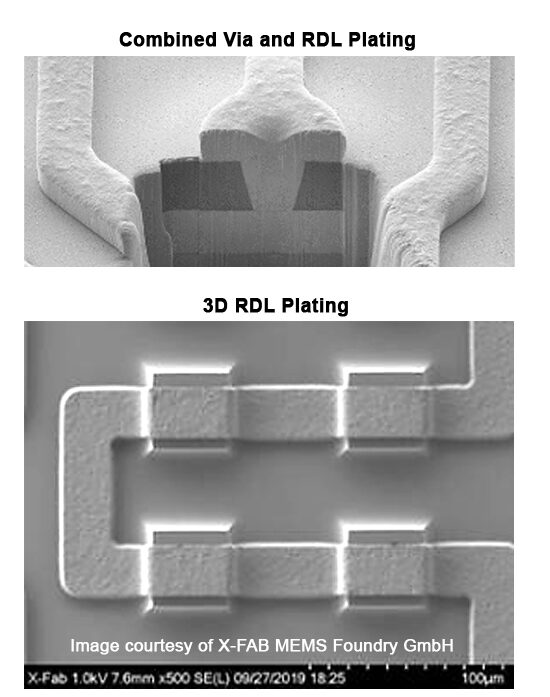
Copper RDL (redistribution layer) plating is a key process step in advanced packaging, requiring plating of line-and-pad features patterned in photoresist. Achieving high plating rates without sacrificing uniformity requires a high-rate copper chemistry, but it’s the chamber design that is critical to achieving both high-quality uniformity and the highest plating rates.
Our proprietary Solstice® CopperMax™ reactor integrates a cationic exchange membrane that separates organic additives from the anode while still allowing high-speed copper cation movement to the wafer. It also dramatically reduces the deterioration of organic additives by using a cationic exchange membrane to keep additives from contacting the anode. This significantly reduces your chemistry costs while enhancing copper plating quality by enabling uniform flow and density distribution of chemistry against the wafer.
The Solstice CopperMax chamber enables higher plating rates while routinely reducing user chemistry costs by more than 95% to deliver excellently plated feature uniformity.
Applications
- Wafer-level packaging
- 2.5D/3D RDL applications
Features
- Wafer rotation control
- Precision tuning of the electric field
- Conservation of costly organic additives
Benefits
- Uniform plated feature shape
- Lower chemistry costs
- Optimized cost of ownership