Optimized
Processing Quality
For electroplating and wafer surface preparation
Advanced and innovative system and reactor design enables the Solstice platform to deliver consistently high levels of semiconductor plating and surface preparation quality across a range of parameters – such as Uniformity, Feature Shape, Step Coverage, Feature Fill, and more…
Uniformity
Cross-Wafer Uniformity
Solstice delivers consistently excellent cross semiconductor plating uniformity (typical: ≤3%) for plated features in all common semiconductor metallization schemes.
This level of uniformity is enabled by ClassOne’s advanced reactor designs which employ Computational Fluid Dynamics (CFD) modeling of electric field profiles to drive uniform current densities across the wafer. Plating uniformity is enhanced by the extremely uniform fluid motion created by high-precision wafer rotation.
The physics of the Rotating Disc Electrode (RDE)* is an important factor in ClassOne’s reactor design. ClassOne plating reactors employ face-down, rotating disc plating which takes advantage of the inherently uniform physics of spinning an immersed wafer. Static wafer systems such as wet benches have intrinsic limitations both in plating uniformity and deposition rates. By contrast, Solstice is able to deliver high uniformity and yield along with high-speed production.
Within-Feature Uniformity
The Solstice’s typical within-feature metal plating uniformity is ≤1%.
The system’s uniform electric field profile – driven by the CFD-modeled reactor design – also aids in enhancing within-feature uniformity. Extremely uniform fluid motion is created by the reactor’s high-precision wafer rotation; and for gold applications, this is further optimized by ClassOne’s proprietary GoldPro reactor which creates a uniquely randomized fluid vector.
Wafer-to-Wafer Uniformity
Solstice delivers typical wafer-to-wafer plating uniformity of <1% for all common metallization schemes.
To achieve this level of uniformity ClassOne uses only the highest-quality high-precision power supplies which are able to deliver extremely high repeatability. Amp-time-driven step termination ensures that precisely the same metal mass is applied to every wafer. An accurate, closed-loop electrolyte flow control also ensures highly consistent mass flow characteristics.
Feature Shape
Plating Feature Shape Uniformity
Solstice is able to deliver extremely high uniformity – down to <1.5% – in plating feature shapes. This includes plated metals that are very sensitive to variations in fluid dynamics, such as gold.
Solstice’s feature-shape plating performance is made possible because of fluid vector control. ClassOne’s proprietary GoldPro reactor, for example, is able to create completely randomized fluid vectors across the wafer surface (illustrated by image at left). This minimizes the thickness of the diffusion layer and eliminates the directionality of fluid against wafer.
In the comparison of plated structures shown in the graph, the unevenness of the feature on the left will jeopardize the quality and reliability of subsequent bonding processes; while the flat feature on the right, plated by Solstice, will promote optimized, reliable bonding.
Feature uniformity plus high plating rates
In this example of gold plating, the Solstice’s ability to ensure randomized fluid interaction at the wafer surface results in an extremely uniform diffusion layer, which ensures that a constant plating rate is maintained throughout.
Note the difference in feature quality produced by the Solstice as revealed by the profiler scans.
The net result is that Solstice is able to deliver very high plating rates while at the same time maintaining excellent feature uniformity.
A 2x roughness improvement
In this gold plating example, the customer’s application called for <50Å deposition, but their process of record (POR) had been 192Å. With Solstice, they were able to achieve a POR of 23Å.
Also, as may be seen in the profile comparison, the customer’s POR had been yielding feature profiles that were not flat and very rough. With Solstice, the features became perfectly flat with a 2x reduction in roughness.
Step Coverage

Solstice >70% step coverage on a >3:1 aspect-ratio structure
Even on challenging applications
Solstice delivers both exceptional step coverage and high plating rates. One example is the >70% step coverage on the >3:1 aspect-ratio structure shown at right.
Solstice is able to achieve this performance because of ClassOne’s proprietary reactor designs, optimized for high rates and uniform deposition. Also, special recipe design can drive gold-complex ions down into the structure to produce the densest possible deposition at the bottom.
Feature Fill
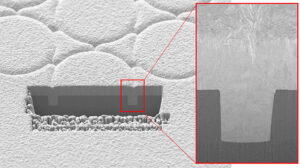
Solstice gold feature fill
Seamless filling
Solstice delivers high-quality void-free fill for a range of challenging applications. These include copper TSVs, gold microLED bond pads, VCSEL contacts, and more. Shown here are typical examples of Solstice’s gold feature fill and a difficult high-aspect-ratio copper feature fill.
The Solstice is able to achieve exceptional void-free feature filling because of its application of state-of-the-art plating waveform technology combined with the use and optimization of best-of-class plating chemistries. Over many years, ClassOne has developed close, mutually beneficial working relationships with all of the industry’s major chemistry and metrology vendors.
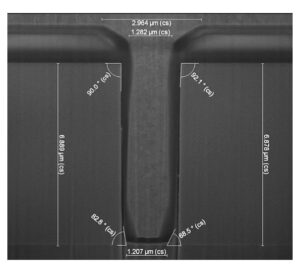
Solstice high-aspect-ratio copper fill